Since PET does not have the required strength in the molten state, PET materials are transformed into hollow tube-like parts which is actually the preform of a bottle. These parts from the injection process are molded in blowing machines and are used to produce different types of bottles depending on the shape of the bottle and the preform weight.
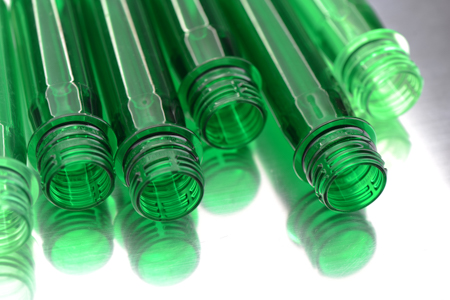
The PET raw materials inside the silo are entered the dryer by material loader pipes and dried for about 2 hours at a temperature of 140 to 170 and transferred to the injection molding machine. These materials are melted during the injection process and injected into the mold. The parts inside the mold are cooled by a chiller and the transparent part is removed from the mold. These parts are transported by conveyor and packed in special bags.
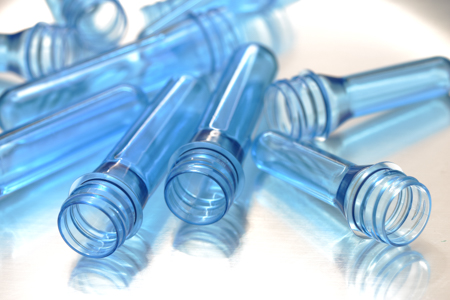